Air separation equipment
Air separation energy storage modular device
The company has developed an energy storage cryogenic air separation device, including feeding system, purification and regeneration system, heat exchange system, rectification system, energy storage system. Specifically, these systems are successively connected: the feeding system is connected with the heat exchange system; the main heat exchanger is also connected with the energy storage system; the energy storage system comprises a first general oxygen storage tank, a second general oxygen storage tank and a pure oxygen storage tank.
To increase the adjustability of oxygen production, this product sets up pure oxygen storage tank and general oxygen storage tank on the basis of traditional air separation process. It stores the liquid generated by the air separation equipment and carries out heat exchange through the pipeline design and heat flow in the air separation process. It also organically integrates the liquid oxygen storage tank which was originally independent of the air separation device into the air separation equipment. In addition, to reduce the energy consumption of air separation, this product uses an efficient air-water cooling system and is integrated into the cold box together with the purification system to reduce the floor area and construction cost.
Technical parameters:
treated gas volume | 2000Nm³/h | 4000Nm³/h | 6000Nm³/h | 10000Nm³/h |
working pressure | 0.45Mpa | 0.45Mpa | 0.45Mpa | 0.45Mpa |
operating temperature | -196℃ | -196℃ | -196℃ | -196℃ |
adjustable load range | 10-100% | 10-100% | 10-100% | 30-100% |
conventional air separation shaft power | 1065KW·h | 2070KW·h | 3060KW·h | 4800KW·h |
save power of air separation shaft | 1020kW·h | 1910KW·h | 2800KW·h | 4500KW·h |
energy saving | 34.38% | 35.65% | 36.14% | 36.33% |
Taking the oxygen production at 2000 Nm³/h as an example, the energy consumption of the traditional cryogenic oxygen air separation process is 1065kW·h. Given the energy storage air separation device provided in this disclosure, the energy consumption is 2700 kW·h at 8-hour valley power and 170kW·h at 16-hour peak and normal power. Although the average energy consumption of the device is 1020 kW·h, which is 45 kW lower than that of the traditional cryogenic oxygen air separation process, it’s important to consider the electricity rates. To put it more specifically, these include the low rate of 0.3393 yuan/degree, the flat section of 0.5494 yuan/degree, and the peak rate of 0.7595 yuan/kW·h, with a peak electricity rate of 0.8646 yuan/kW·h.
The annual electricity cost of the traditional cryogenic oxygen air separation process is about 5.1247 million yuan, while the annual electricity cost of using the energy storage air separation device is about 3.3628 million yuan, which leads to a saving of 34.38% in electricity costs.
Equipment advantages:
1.Set the liquid-air storage tank and liquid oxygen storage tank to store cold capacity during off-peak hours and provide it for equipment operation during peak hours, thereby reducing energy consumption.
2. Through the rectification system, heat exchange system and energy storage equipment in the equipment to optimize the exchange of cold and hot flows, ensuring high efficiency and energy savings.
3. Solves the complexity of start-stop operation of traditional air separation equipment, realizing one-button operation, reducing start-up time, and quickly reaching the required concentration of products.
4. During operation, the product quality is stable. Once purity levels drop below standard, the intelligent storage can be switched to prevent the loss of pure accidents and improve the operation efficiency.
Cryogenic film method oxygen enrichment device
The oxygen enrichment device is a set of low-cost oxygen enrichment equipment, low operating pressure - 0.15Mpa, low energy consumption - 0.08KWh/m³ oxygen enriched air (40% oxygen content). The device uses liquid air to create a liquid film at low temperatures. When the air from the blower passes through the liquid film, more oxygen components remain in the liquid to achieve the purpose of oxygen enrichment. The device is designed for skid loading, and the purification precooling equipment is built in the cold box. The blower through the system has low resistance, small pressure drop, no need for secondary supercharging air supply, reducing equipment investment.
Technical parameters:
Equipment model | MDO-1000 | MDO-3000 | MDO-10000 | MDO-15000 |
Output Nm3/h | 1000 | 3000 | 10000 | 15000 |
KPa | 50 | 50 | 50 | 50 |
Oxygen content | 40% | 40% | 40% | 40% |
Load regulation range | 20%-110% | 20%-110% | 20%-110% | 20%-110% |
Powe | 90 | 255 | 820 | 1200 |
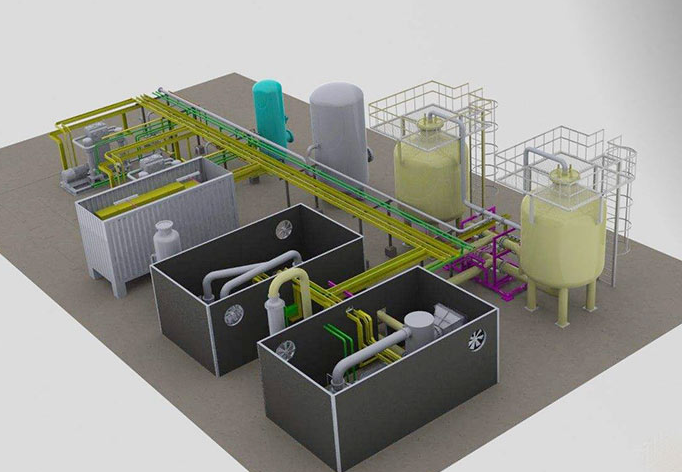
Krypton-xenon roughing equipment
Horizontal krypton-xenon separation equipment represents an innovation in the traditional vertical rectification tower. It uses horizontal rectification, vacuum and low-pressure separation techniques for krypton-xenon. Special materials are employed to ensure the insulation performance of the equipment. Also, the design of efficient single condensation evaporation circulator helps reduce energy loss, improve heat transfer efficiency, so as to achieve the reduction of energy consumption of the equipment. Besides, the horizontal rectification tower also comes with small footprint, energy saving effect and other advantages.
Technical parameters:
treated gas volume
|
pressure | operating temperature | adjustable load range | krypton concentration | xenon concentration | extraction ratio |
3000Nm³/h | <50KPa | -183℃ | 30-100% | 3000ppm | 3000ppm | ≥98% |
Equipment advantages:
1.On the basis of the original krypton-xenon system, a fractionating tower is added, and the heat transfer mode of cold and heat flow is set up reasonably.
2. Compared with traditional krypton-xenon refining equipment, the cold source changes from liquid nitrogen to liquid oxygen, while reducing the consumption of cold source to 40%.
3. No pressure nitrogen precise temperature control, stable and reliable operation with minimal fluctuations in working conditions.
4. Fundamentally avoid the curing of krypton xenon in traditional technology, and effectively solve the problem of pipeline blockage.
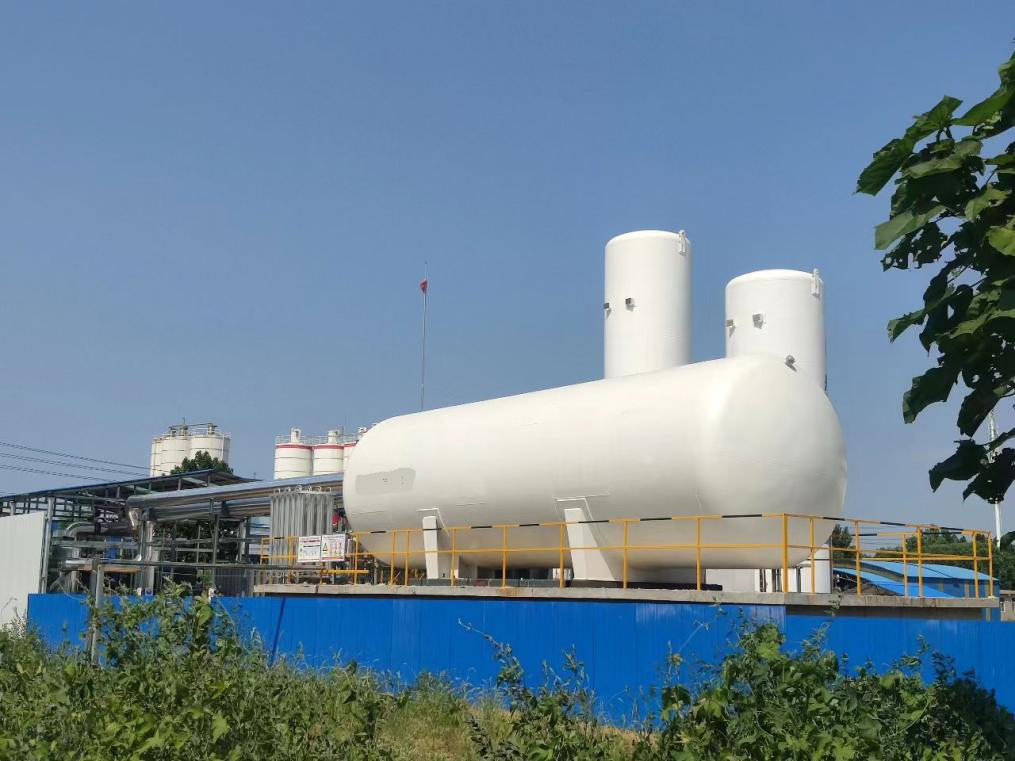
Krypton-xenon refining equipment
Technical parameters:
treated gas volume | pressure | operating temperature | krypton concentration | Xenon concentration |
400Nm³/h | 0.2Mpa | -183℃ | 99.999% | 99.999% |
Equipment advantages:
1. Five-tower separation, well-organized process layout, adding a 5# krypton-xenon liquid concentration tower. This tower enables concentration below 5% without cold source and heating evaporation, which reduces energy consumption..
2. Compared with the traditional krypton-xenon refining equipment, the cold source is changed from liquid nitrogen to liquid oxygen, and the consumption of the cold source is only 50% of the original.
3. High stability, no pressure nitrogen precise temperature control, stable and reliable operation with minimal fluctuations in working conditions.
4. The self-balance of evaporation and condensation process is used to reduce operational difficulties.
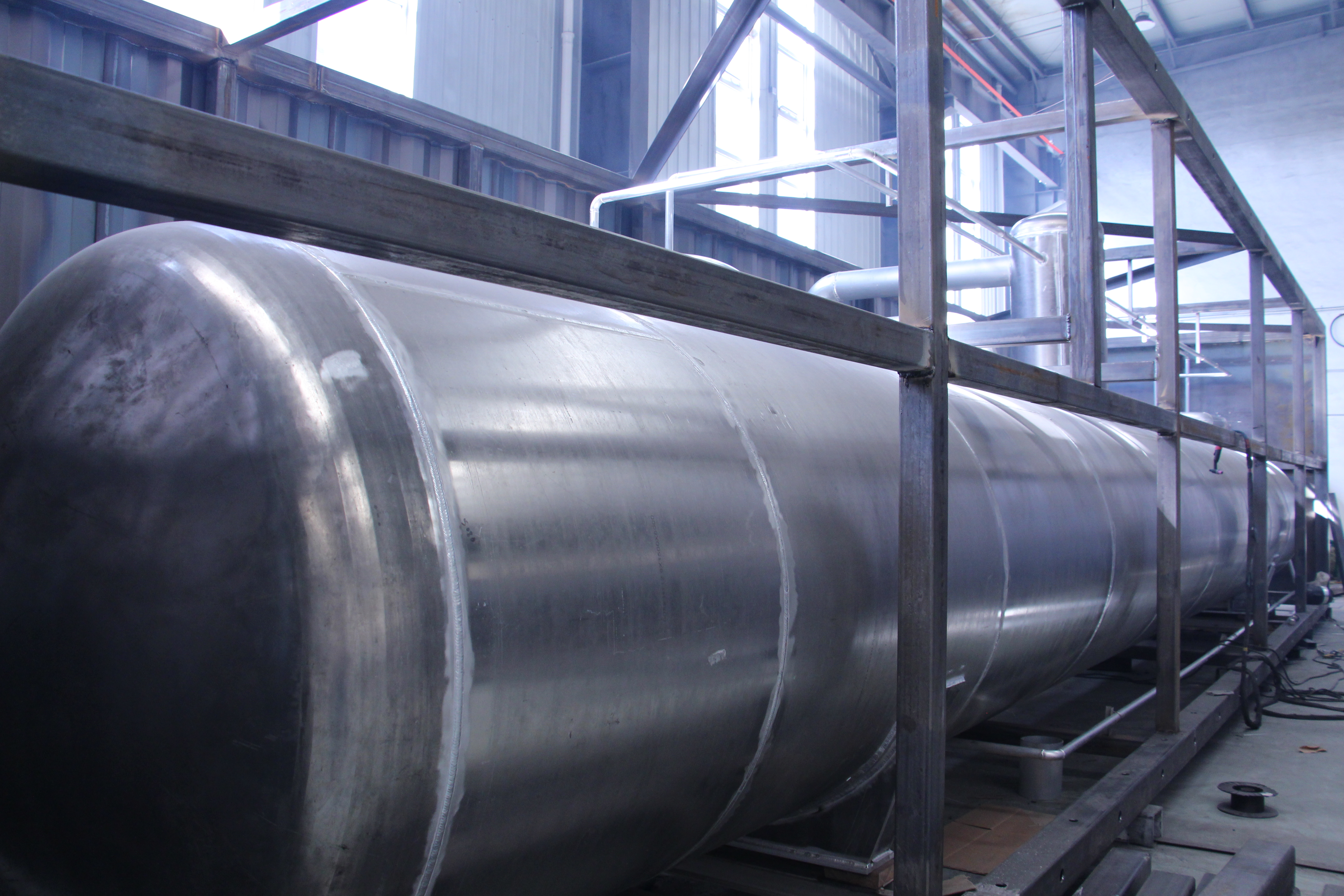
Nitrogen roughing equipment
The non-condensing steam discharged from the air separation tower enters the neon-helium cold box, and exchanges heat with the reflux low-temperature raw gas and returned nitrogen through the main heat exchanger. After being cooled to the saturation temperature, it enters the rectification tower and further separates into raw gas and liquid nitrogen.
Equipment adopts upper and lower double main cooling design, plate heat exchanger efficient heat exchange, hot end temperature difference is less than 3℃, high efficiency condensing evaporator evaporates liquid oxygen at the same time liquefied air, heat transfer temperature difference of 1.2℃. The liquid nitrogen consumption is small, the operation is stable, and the extraction rate is high.
Equipment advantages:
1. Skid mounted design, small footprint, easy inspection and maintenance.
2. Small cold loss, less power consumption.
3. High concentration rate and high extraction rate of neon helium.
Main technical performance indicators:
Equipment type | Processing gas volumeNm3/h | content | Installed power KW | Liquid nitrogen consumption |
XDNEHE-100 | 100 | 58.6% | 20 | 30L/h |
XDNEHE-200 | 200 | 58.6% | 35 | 50L/h |
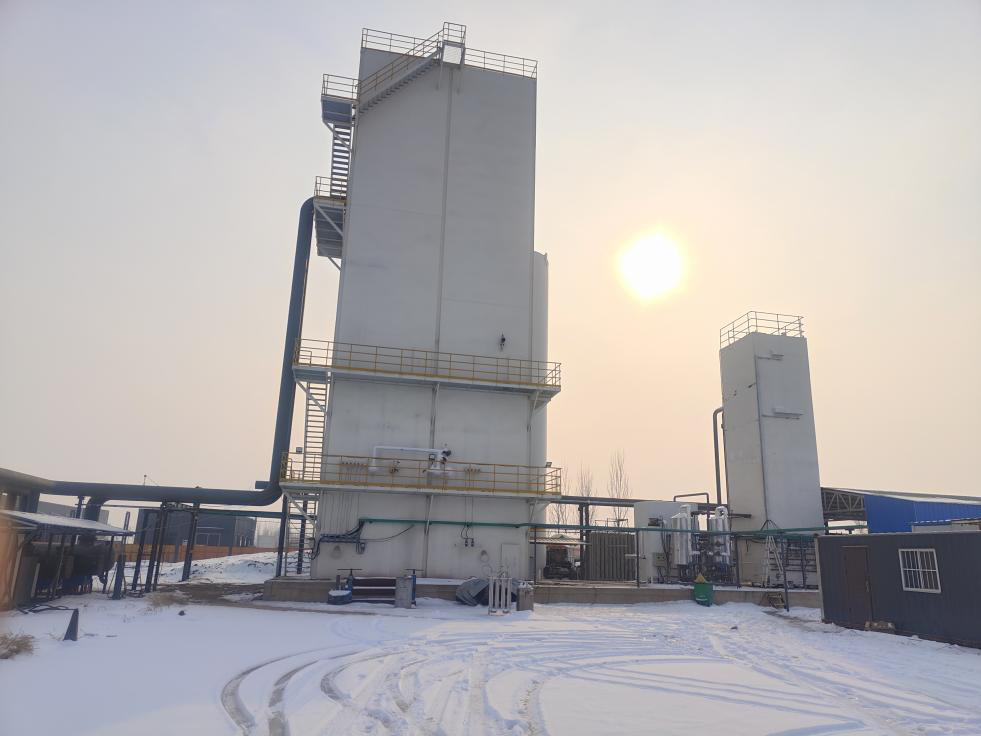
Nitrogen gain vaporizer - cold energy recovery device
Technical parameters:
treated gas volume | pressure | operating temperature | adjustable load range | nitrogen concentration | installed power |
200Nm³/h | 0.8MPa | -196℃ | 0-100% | <10ppm | 50KW |
400Nm³/h | 0.8MPa | -196℃ | 0-100% | <10ppm | 97KW |
800Nm³/h | 0.8MPa | -196℃ | 0-100% | <10ppm | 130KW |
Equipment advantages:
1.The gain vaporization developed by the company stands as a perfect substitute for the traditional empty bath vaporization, which solves the problem of wasted cold capacity in conventional setup.
2. Nitrogen purity can be guaranteed at 99.999%.
3. High utilization rate of cold capacity, converted into nitrogen, reducing the purchase of liquid nitrogen by 20-30% and overall cost savings.
4.The whole equipment is container-type, small size and features high utilization rate, which make it easy to move and install.
5. It offers high self-control, allowing for flexible dosage adjustment and immediate use.
6.Low temperature media such as LNG/LN2/LO2 can also be recovered.
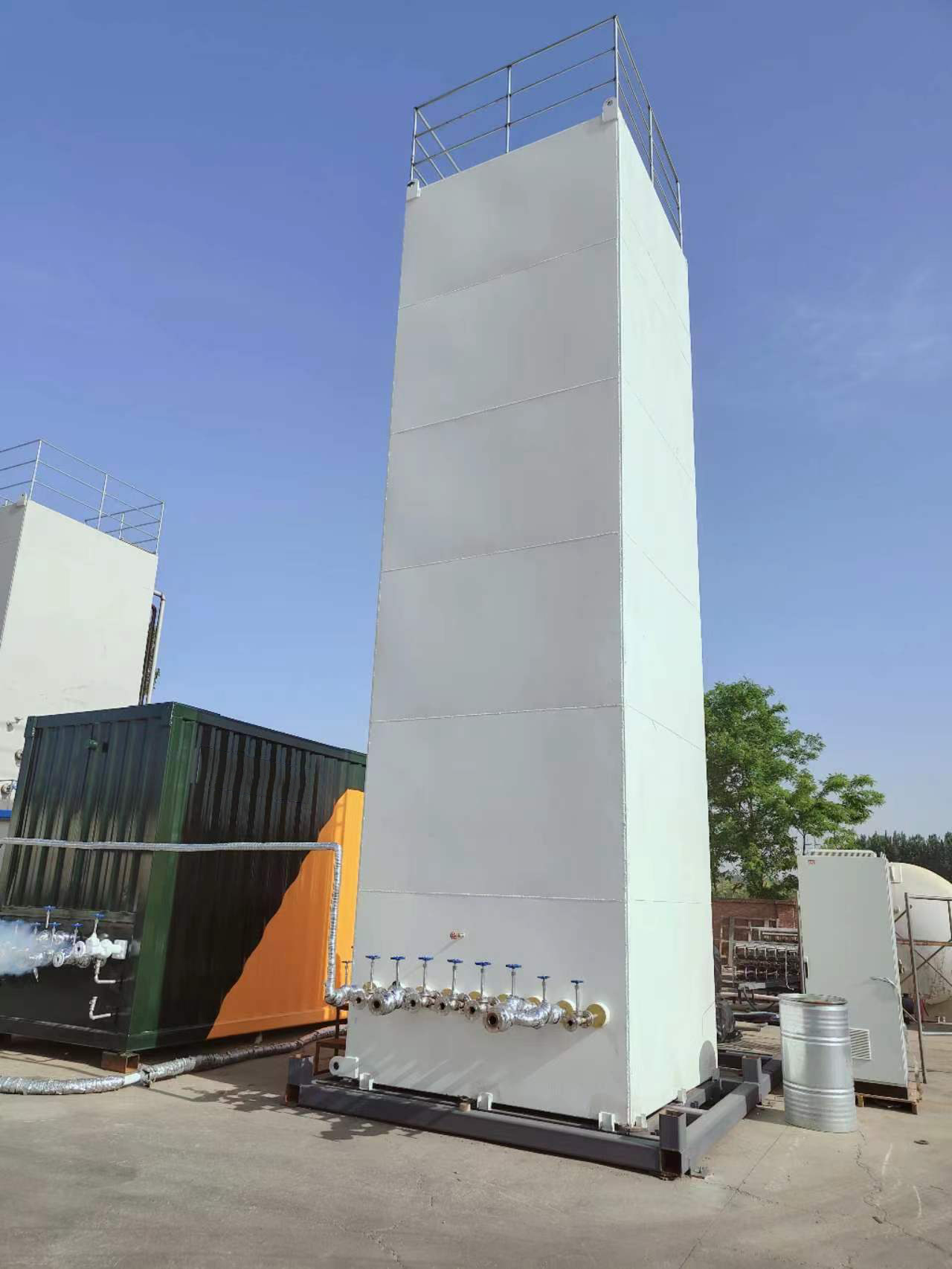